Screw Compressor
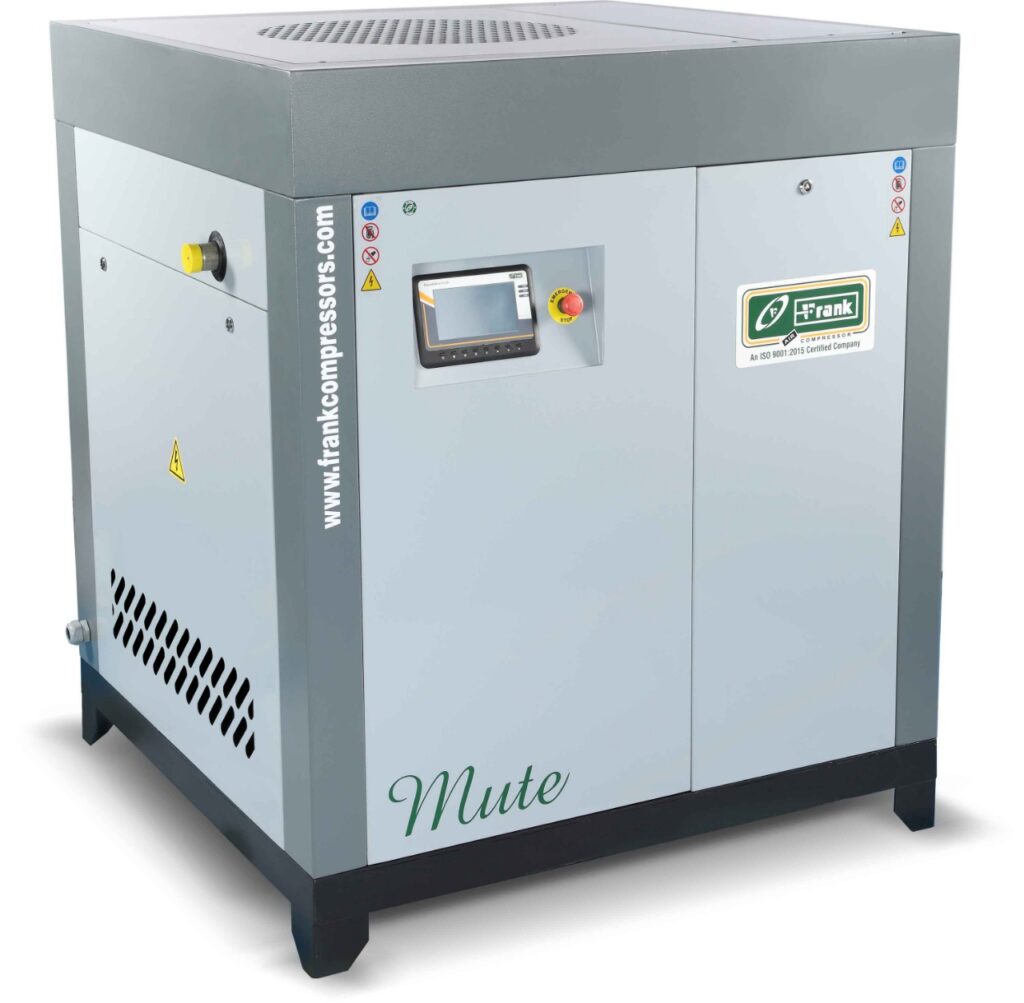
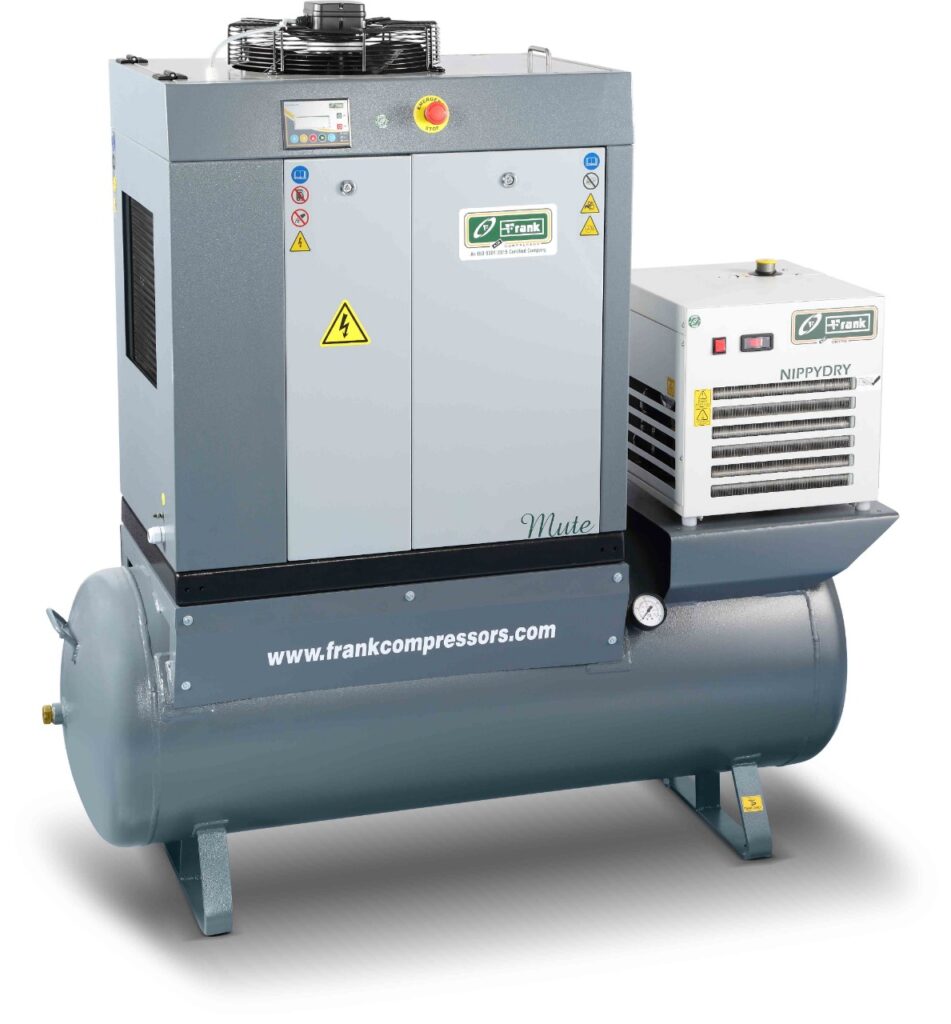
Screw Compressor
Frank screw compressor is designed for “easy maintenance” which means that compressor will enable service person to reach each component easily. our design with full of engineering advantages allows lower prices and higher performances. Quality, reliability and economy are basic determining factors of our compressors. Our design allows no professionally or additional staff for servicing the basic components of the compressors. The compressors manufactured around the year 2000 were having complexity and other problems. Frank solved this with new design basics allowing less service time and higher efficiency at different conditions.
This allows no professionally or additional staff for servicing the basic components for the compressors. The compressors manufactured around the year 2000 were having complexity and other problems. Frank solved this with new design basics allowing less service time and higher efficiency at different conditions. Frank’s vision became a solid philosophy for all Frank products and created a different view at Rotary screw market that allowed all Frank products to be exported all around the world.
Energy Efficient Screw Air Compressor
- Advanced screw air end
- Intelligent microprocessor based electronic controller
- Three stage air oil separator
- Low specific power consumption
- Less noise level and ease of maintenance
- Very Compact
Excellence In Integrated Air Dryer
- Foot print required is less as compressor and dryer mounted on the air tank.
- Huge money and time saved by avoiding site plumbing and electrical.
- Compressor and dryer are independent hence dryer maintenance is possible without stopping the compressor. Therefore no production losses.
- Single transport cost.
- Plug and use on arrival of the compressor.
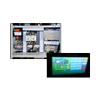
Micro Computer Control System
- Intelligent micro computer control system. The LCD can show present temperature, working pressure, accumulative working time, malfunction, etc. Maintenance schedule through ON Line.
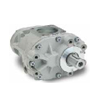
Advanced Screw Airend
Advanced rotary screw technology, equipped with high efficiency rotary screw airend powered by efficient electric motor.
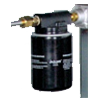
Oil Filter
The screw spin on oil filter makes servicing convenient. The filter eliminates oil impurities and other particles produced by wear and tear. High quality oil filtration extends the service life of rotors, bearings and other moving parts.
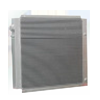
Energy Efficient Combination Cooler
Utilising production methods and design the cooling system was designed to provide sustainable and efficient operation in high temperature high humidity environments. The new cross-exchange cooler not only increases exchange capacity by 10% but also is designed to resist chemical damage.
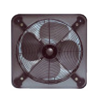
Quite Operation
High efficiency cooling fan provides sound level low.
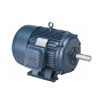
Motor
World-class IE2 electric motor features Grade F insulation and IP54 protection. Bearings are SKF
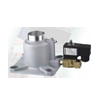
Loading Head
This newly designed and improved intake controll system ensures economic control and protection of the screw. The control system has been redesigned to be simpler and more reliable. The air intake filter eliminates dust and other harmful particles that may cause premature wearing of the machine. Upon start-up of the machine, the control system will close the intake valve reducing start-up load. Shut down procedure will release pressure from the oil reservoir and prevent lubricant leakage. The new design has resulted in reduced air intake noise.
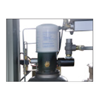
Spin on Three Stage Separator Air/Oil
Service & maintenance are made extremely simple through spin on three stage separator (upto 20 HP) and convenient location of oil receiver, oil filters and air oil separator – user friendly from servicing point of view. The separator will remove oil particles from the air down to a ratio of 1-2 parts per million. Efficient separation means post-treatment of all will be economical. Cleaner air means low maintenance costs on pneumatic equipment.
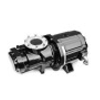
Magnetic Motor
By using permanent magnet synchronizing motor the energy saving on the VSD can be increased by 15 to 20%. Permanent magnetic motor and compressors are designed with the one shaft and by 100% transmission efficiency. Compared to normal motor the permanent magnet synchronizing motor performs with the excellent energy efficiency.